Idee
Für kleinere Bilder, Fotos etc. benötigt man häufig einen passenden Bilderrahmen, um das Foto, die Zeichnung o.ä. ansprechend präsentieren zu können.
Als Besitzer eines 3D- Druckers ist es daher naheliegend sich mithilfe von CAD- Software selbst einen Bilderrahmen zu entwerfen und dann auf dem 3D- Drucker auszudrucken.
Gleichzeitig ist der CAD- Designprozess eine gute Übung für das Arbeiten mit der in aller Regel sehr komplexen CAD- Software.
Als Vorlage für das eigene Design diente in diesem Fall ein bereits vorhandener Bilderrahmen aus Holz im Kleinbildformat ca. 140 x 140mm:
Design
Ausgehend vom vorhandenen Objekt wurden zunächst entsprechende Fotos vom Objekt aufgenommen und mit den für das Design relevanten Bemaßungen versehen:
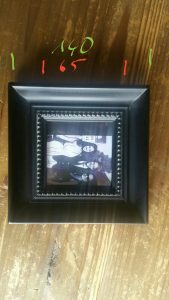
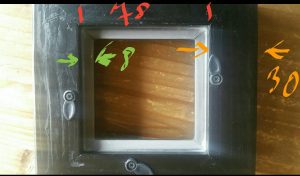
Als CAD- Software nutze ich Fusion 360. Die Software bietet u.a. auch die Möglichkeit, Konstruktionszeichnungen anhand von Fotos von bestehenden Objekten zu erstellen.
Fotos als Vorlage für Konstruktionszeichnung
Dazu importiert man die Fotos als ‚Angehängter Ansichtsbereich‘ in das Fusion360- Design. Anschließend müssen die importierten Bilder über die entsprechende Funktion kalibriert werden, d.h. die Konstruktionszeichnung wird anhand einer Maßangabe am Foto justiert.
Für die Zeichnung habe ich 2 Bilder importiert als Front-Ansicht und Seitenansicht. Die beiden Bilder müssen nach dem Import noch dem jeweiligen Koordinatenraum zugeordnet werden.
Basierend darauf habe ich dann die entsprechende Konstruktionszeichnung des Rahmenprofils (Querschnitt des Rahmenelement) angefertigt:
Das Profil wurde über die Versatz- Funktion im Zeichnungsdialog von F360 in der Wanddicke zunächst auf 1 mm festgelegt. Das bedeutet, dass die Extrusion des Profils Hohlkörper mit der Wanddicke von 1mm erzeugt.
Extrusion und Positionierung der Einzelteile
Die Extrusion des Profils wurde dann als symmetrische Extrusion mit jeweils 30mm ausgeführt:
Das so geschaffene gerade Stück des Rahmens wurde in F360 mittels Copy & Paste in benötigter Anzahl kopiert. Ferner wurden zwei Konstruktionsebenen erzeugt, die für die 45° Teilung der Geraden benötigt wurden, also ein +45° Ebene und eine -45° Ebene. daraus sind dann die Eckstücke des Rahmens erzeugt worden:
Nachdem die erste Gerade und das erste Eckstück erstellt worden sind, konnten Kopien der Körper erzeugt werden und durch Rotation und Verschiebung an die geeigneten Positionen im Raum dann der komplette Rahmen aus den einzelnen Körpern zusammengesetzt werden. Durch das Kombinieren der Einzelkörper wurde dann eine neue Komponente erzeugt, die den schon fast fertig gestellten Rahmen darstellt:
Rückseitenprofil
Da aus dem Rahmenprofil jeweils Hohlkörper erzeugt wurden, musste auf der Rückseite noch eine Lösung für die Aufnahme des Bildobjektes geschaffen werden:
Rückseite unvollständig durch Extrusion des Hohlkörpers
Um dieses Problem zu beseitigen wurde ein separater Körper konstruiert , der dann in den entstandenen Hohlraum eingesetzt wurde:
Verzierung des Ausschnittsfensters
Im Ausschnittsfenster auf der Vorderseite des Rahmens sollte nun noch eine umlaufende Verzierung eingefügt werden. Dazu wurde zunächst ein Halb-Kugelelement auf dem Ausschnittsfenster erzeugt und positioniert:
Mit Hilfe der Fusion360 – Funktion ‚Anordnung auf Pfad‘ lassen sich Körper auf Pfaden in beliebiger Menge und beliebigem Abstand zueinander anordnen. Eine Funktion, die sich hier als sehr hilfreich erweist. Damit konnte aus dem einen Halbkugelelement die entsprechende Menge der Verzierungen in rechteckiger Anordnung auf dem Fensterausschnitt der Frontseite angeordnet werden:
Rückseitendeckel, Verschlussplatten und Rahmenaufsteller mit Scharnier
Damit die auf die Rückseite aufgebrachten Objekte von hinten befestigt werden, musste nun noch ein Deckel für die Rückseite konstruiert werden. Ferner sollte noch ein entsprechend dimensionierter Rahmenaufsteller kreiert werden, der dann als Klappaufsteller über ein entsprechendes Scharnier an die Rückseite des Bilderrahmens angebracht werden kann.
Die Rückseite wurde als rechteckige Fläche mit einer Dicke von 2mm als separater Körper entsprechend den Abmaßen des rückseitigen Ausschnitts extrudiert. Zur befestigung des Aufstellers wurden 2 kleine Löcher im Abstand von 7 mm berücksichtigt:
Auf gleicher Ebene wurde dann der Aufsteller gezeichnet und ebenfalls als separater Körper mit einer Dicke von 2 mm extrudiert:
Für die Befestigung des Aufstellers an der Rückseite habe ich mich für ein Klapp- Scharnier entschieden, damit der Aufsteller auch platzsparend an den Rahmen angeklappt werden kann.
Das Scharnier habe ich nicht selbst konstruiert sondern auf ein auf thingiverse verfügbares Teil zurückgegriffen: https://www.thingiverse.com/thing:2187167
Dieses Scharnier kann über OpenSCAD beliebig nach den verschiedensten Kriterien konfiguriert werden und dann als STL- File erzeugt werden. Ich habe bei der Erzeugung zunächst folgende Parameter in OpenSCAD angegeben:
Ein kleines Scharnier, dass dann an den Aufsteller und die Rahmenrückseite angebracht werden kann.
Die 19mm langen Verschlussplatten zur Befestigung des Deckels der Rückseite wurden in F360 gezeichnet und dann mit einer Dicke von 1mm extrudiert:
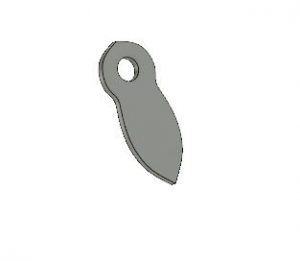
Für die Befestigung auf der Rückseite des Rahmens werden 4 dieser Teile benötigt, die dann mit kleinen Schneidschrauben auf der Rückseite befestigt werden:
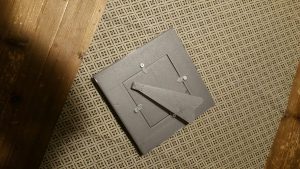
Druck des Bilderrahmens
Der Druck des Rahmens in Originalgröße von ca. 157 x 157 mm sollte problemlos auf jedem handelsüblichen 3D- Drucker mit den entsprechenden Druckbettabmessungen möglich sein.
Besonderes Augenmerk sollte auf die Support-Strukturen gelegt werden, da aufgrund der Überhänge der Rahmenelemente und Hohlkörper nicht ohne Supportstrukturen gedruckt werden kann. Für einen ersten Entwurf habe ich die Dichte der Supoortstrukturen zunächst auf 5 % festgelegt und das Füllmuster auf Triangles. Damit werden auch die Verbrauchskosten für das Filament reduziert. Als Druckauflösung habe ich zunächst 0.3mm Auflösung gewählt (bei 0.4 mm Düse). Die weiteren relevanten Druckparameter können dem folgenden Bild der Cura- Einstellungen entnommen werden:
Mit diesen Einstellungen dauerte der Druck auf meinem anycubic i3 mega in PLA grau bei 80mm/s Printspeed ca. 5 Stunden 45 Minuten. Das Ergebnis kann sich für einen ersten groben Entwurf durchaus sehen lassen:
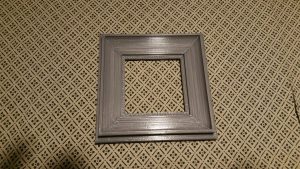
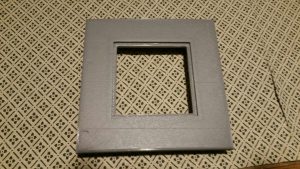
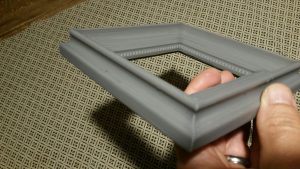
Druck der weiteren Teile des Bilderrahmens
Die Rückseite und der Rahmenaufsteller lassen sich aufgrund der geringen Dicke sehr einfach und schnell mit Standardeinstellungen drucken. Weder Supportstrukturen noch Brim oder Raft sind hier notwendig.Die Druckauflöung muss hier nicht besonders hoch sein, ich habe hier mit 0.3mm Auflösung gedruckt bei 80mm/s Printspeed und beide Teile waren nach jeweils ca. 20 Minuten gedruckt.
Das kleine Scharnier sollte mit hoher Auflösung gedruckt werden, damit es nach dem Druck auch rotiert werden kann. Ich habe mit 0.1mm Druckauflösung bei reduzierter Druckgeschwindigkeit von 40mm/s sehr gute Erfahrungen gemacht.
Die Verschlussplatten können in der benötigten Menge gemeinsam gedruckt werden. Auch hier sollte mit hoher Auflösung gedruckt werden, da die Teile sehr klein dimensioniert sind. Die Drcukgeschwindigkeit sollte ebenfalls entsprechend reduziert werden. Auch hier habe ich mit 0.1mm Druckauflösung und 40mm/s Printspeed gute Erfahrung gemacht.
Zusammenbau
Der Zusammenbau der gedruckten Teile ist schnell erledigt. Auf den Rückseitendeckel das Scharnier entsprechend den vorgestanzten Bohrlöschern plazieren und befestigen. Ich habe hier zunächst auf Schrauben verzichtet und stattdessen Sekundenkleber benutzt. An das andere Ende des Scharniers dann den Aufsteller befestigen (schrauben oder kleben):
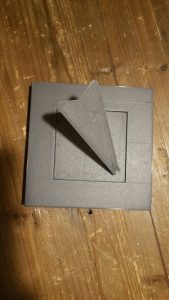
Nachdem dann die vier Verschlussplatten an der Rückseite angeschraubt wurden und das Objekt in den Rahmen eingesetzt wurde, präsentiert sich der fertige Bilderrahmen in voller Schönheit:
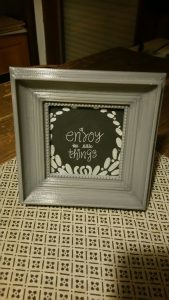
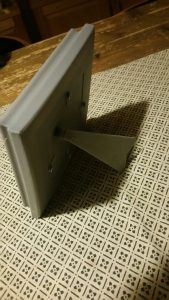
Download der 3D-Files
Alle zum Zusammenbau benötigten Teile für den 3D- Druck ( mit Ausnahme des Scharniers ) sind auf thingiverse unter folgendem Link frei verfügbar:
https://www.thingiverse.com/thing:3597522
Bitte beachtet, die dort festgelegten Lizenzbestimmungen. Der dort frei verfügbare Bilderrahmen ist auf der Rückseite mit einem Schriftzug (meine Web-Adresse) versehen. Dieser Schriftzug darf entsprechend der Lizenzbestimmungen nicht entfernt oder verändert werden.
Sollte Interesse an einem STL-File ohne diesen Schriftzug bestehen, kann dieses gerne bei mir angefragt und käuflich erworben werden.
Kommentare